Outdoor Product Manufacturing and Sourcing Services
The collaborative synergy between design agencies and factories is integral to the success of both the industrial design and product sourcing processes.
By working with factory partners early and integrating manufacturing insights into the design phase, our team is able to create innovative, cost-effective, and high-quality products. This collaboration starts with an open dialogue, where the design team and the factory share knowledge about production capabilities, material constraints, and technological advancements. Our early communication along with our product manufacturing services allow for a seamless transition from the design phase to production.
The collaborative synergy between design agencies and factories is integral to the success of both the industrial design and product sourcing processes.
By working with factory partners early and integrating manufacturing insights into the design phase, our team is able to create innovative, cost-effective, and high-quality products. This collaboration starts with an open dialogue, where the design team and the factory share knowledge about production capabilities, material constraints, and technological advancements. Our early communication along with our product manufacturing services allow for a seamless transition from the design phase to production.
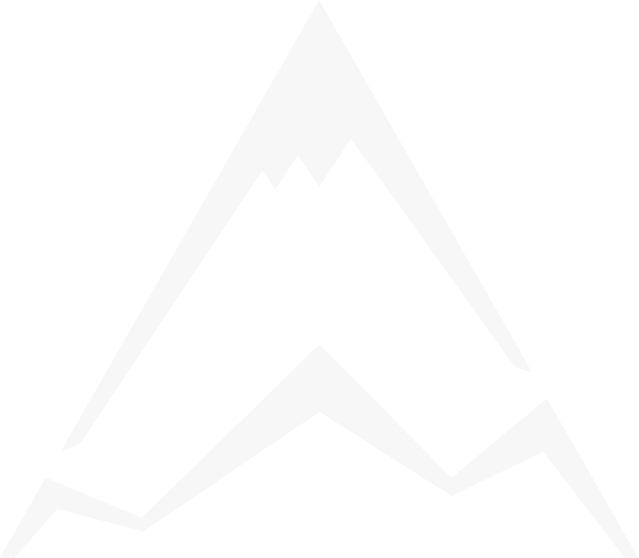
Integrating manufacturing insights into the design process offers numerous benefits. Early involvement of manufacturers in our process allows us to gain valuable insights into the feasibility of a design, see opportunities for optimization, and avoid potential roadblocks.
- Improved Feasibility and Cost-Effectiveness: By considering manufacturability during the design phase, design agencies can create products that are easier and less costly to produce. This optimization ensures that the final products align with market demands while meeting cost targets.
- Optimized Material and Process Selection: Early input from manufacturers helps in selecting the most suitable materials and processes, thereby setting realistic target costs for production. By choosing the right materials and processes upfront, design agencies can avoid costly revisions and delays later in the production cycle.
- Reduced Need for Design Revisions: Collaborating with the production team significantly improves production cycles by streamlining communication, reducing lead times, and facilitating iterative sampling loops. By addressing potential manufacturing challenges early on, we can streamline the design-to-manufacturing process, keeping the product development timeline on track.
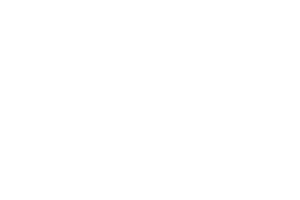
Moreover, the partnership between design agencies and factories can substantially impact product quality. By identifying proper materials and manufacturing processes early, the design team can account for material & process constraints and maintain proper aesthetic and functional standards.
The relationship between a design agency and a factory involves numerous considerations both in the United States and in the Far East. Design agencies typically collaborate with factories to translate creative and technical specifications into physical products. This collaboration can take different forms based on the factory’s location and the type of production process required.
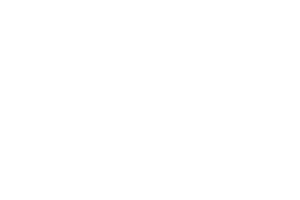
Domestic Manufacturing in the US
Domestic partners offer several benefits, such as closer proximity for easier quality checks, faster turnaround times, and more efficient communication. While easier access to process reviews can be a major advantage, domestic production is often more costly due to higher labor and production costs. The US is known for advanced manufacturing sectors like aerospace, automotive, and microcircuits, requiring sophisticated tools and specialized training.
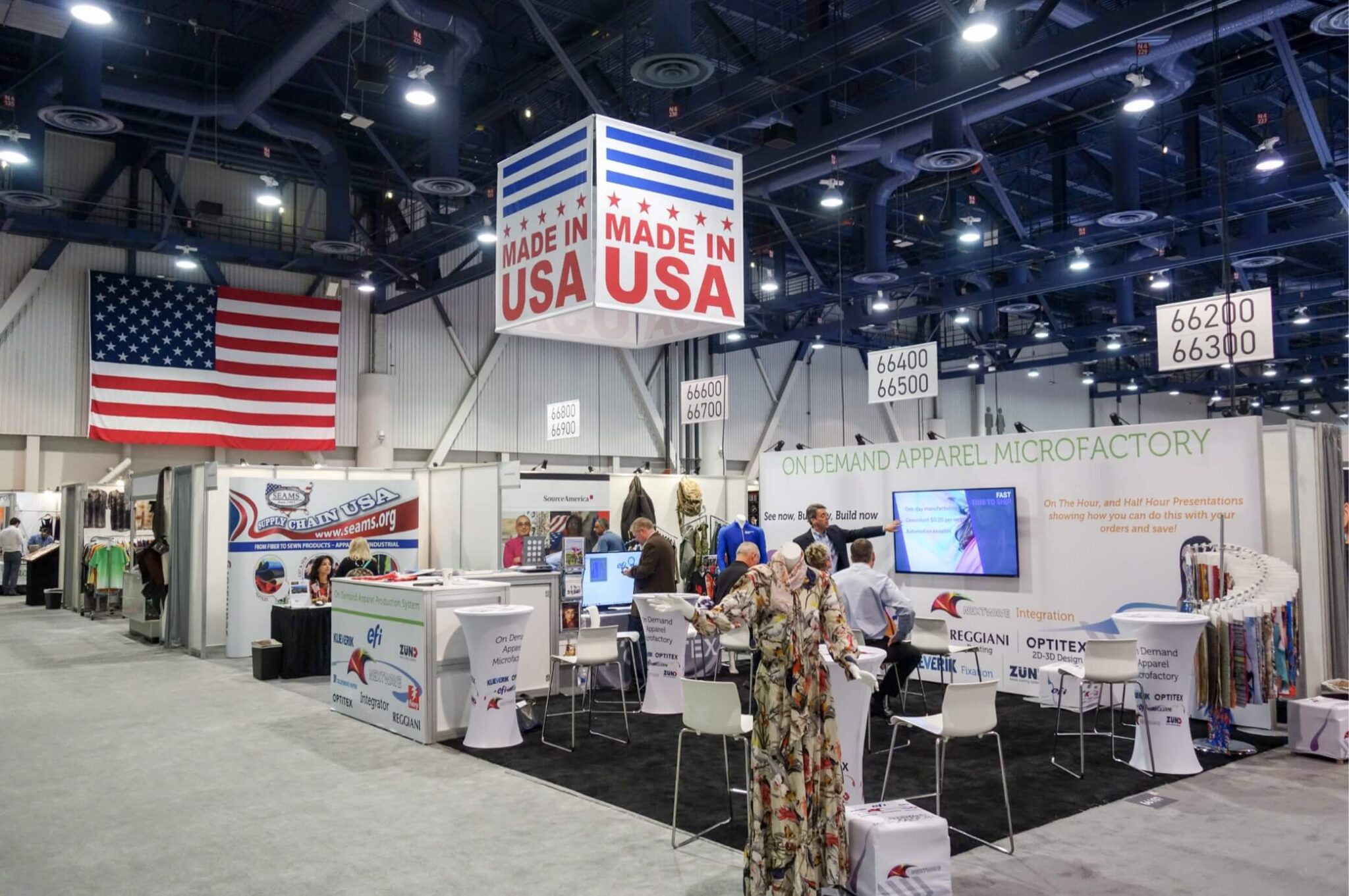
Far East Manufacturing
In contrast, Far East partners, particularly in countries like China, Vietnam, and Thailand, often offer higher cost savings due to lower labor costs. These regions are highly suited for large-scale production of electronics, textiles, and consumer goods. However, challenges such as longer lead times, potential quality control issues, and complexities in logistics and communication can arise. Digital technology plays a significant role in the manufacturing process, enabling multinational companies to distribute different manufacturing processes across various countries. This distribution helps optimize production efficiency and cost but requires careful management of the supply chain and production timelines.
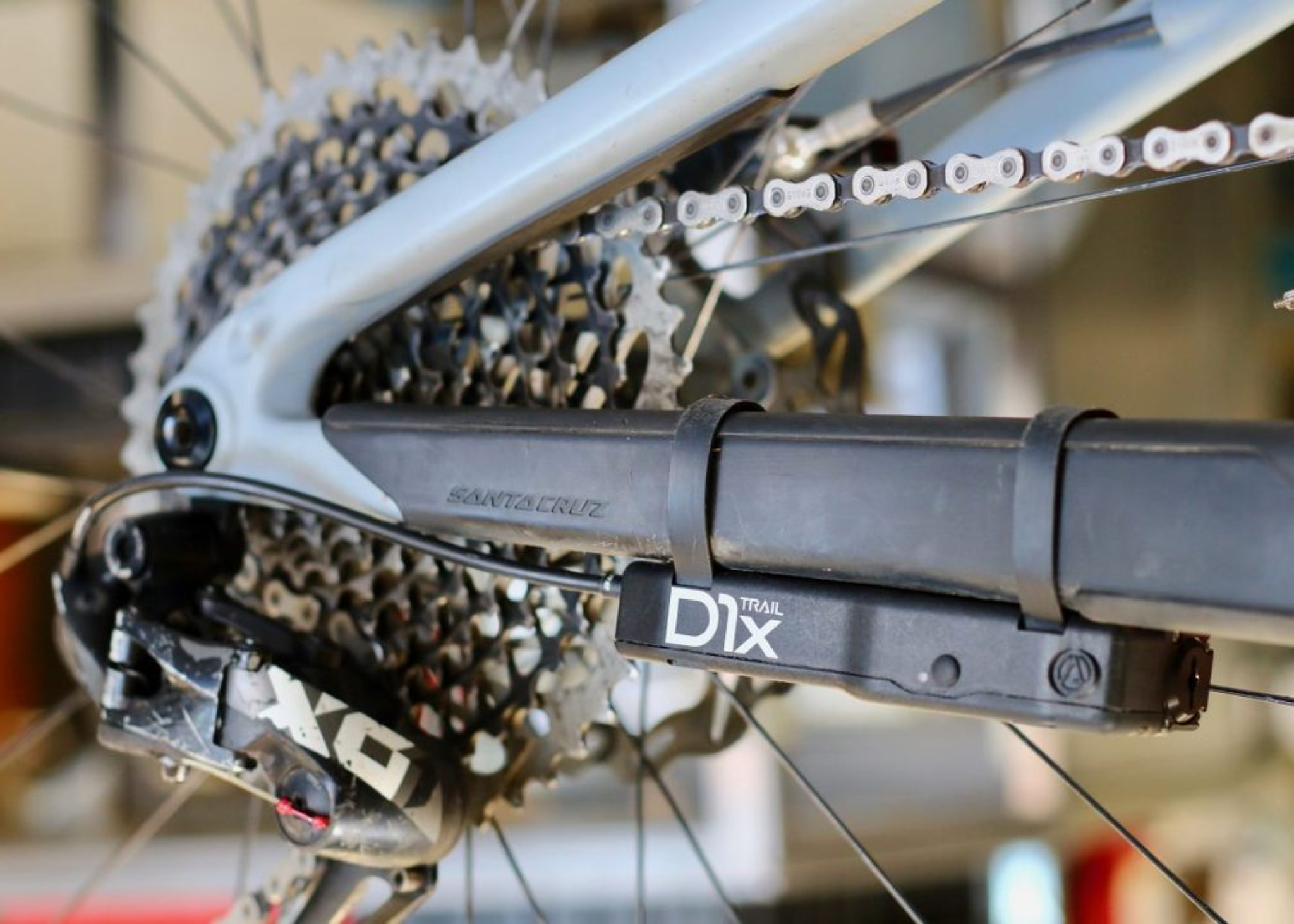
How to Choose
Ultimately, the choice between domestic and international manufacturing depends on a company’s specific needs, including budget, quality requirements, and production volume. Both options have their advantages and drawbacks, and companies must weigh these factors carefully to determine the best strategy for their manufacturing needs. Our team has brought a diverse range of products to market, so we have a wide network of factories, both domestic and overseas. If you’re interested in seeing some of the product categories we have expertise in, feel free to learn more about our team and the products we’ve brought to market.
Our collaboration with factories is essential for creating innovative, cost-effective, and high-quality products. By integrating manufacturing insights into the design process, both parties can ensure that the final products align with market demands, meet quality standards, and optimize production cycles. This collaborative synergy enhances the overall efficiency and effectiveness of the product development process, driving success and competitiveness in the market.
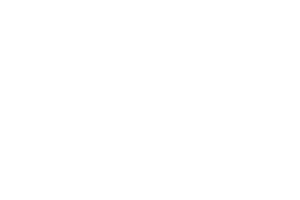
Manufacture and Source with Trailside Creative
When choosing a production partner, it’s important to understand the specific strengths of different regions, the impact of digital technology on production processes, and the need for effective communication and management in maintaining quality and efficiency across diverse manufacturing landscapes. Of course, you can always lean on our product manufacturing services to take care of the manufacturing and sourcing operations details while focusing on your business. Contact our knowledgeable and efficient team today to get started.
While experimentation is laced throughout our entire process, there are three primary feedback zones:
- Concept Testing
- Ergonomics Testing
- Functional Testing
Concept Testing
Whether done internally with our team or externally with consumers, we always test concepts in 2D before committing to a particular concept direction. This process provides a cost-effective way for multiple design iterations to be created rapidly, enabling designers to explore a wide range of possibilities in a short amount of time.
Early-stage 2D concept images can be shared with stakeholders, team members, or potential users to gather feedback before investing time and resources into more detailed development. Based on feedback, our designers can make quick adjustments and refine concepts early in the process. Choosing a concept direction in 2D lowers the risk of needing to backtrack during development, and allows us to consistently deliver products on time.
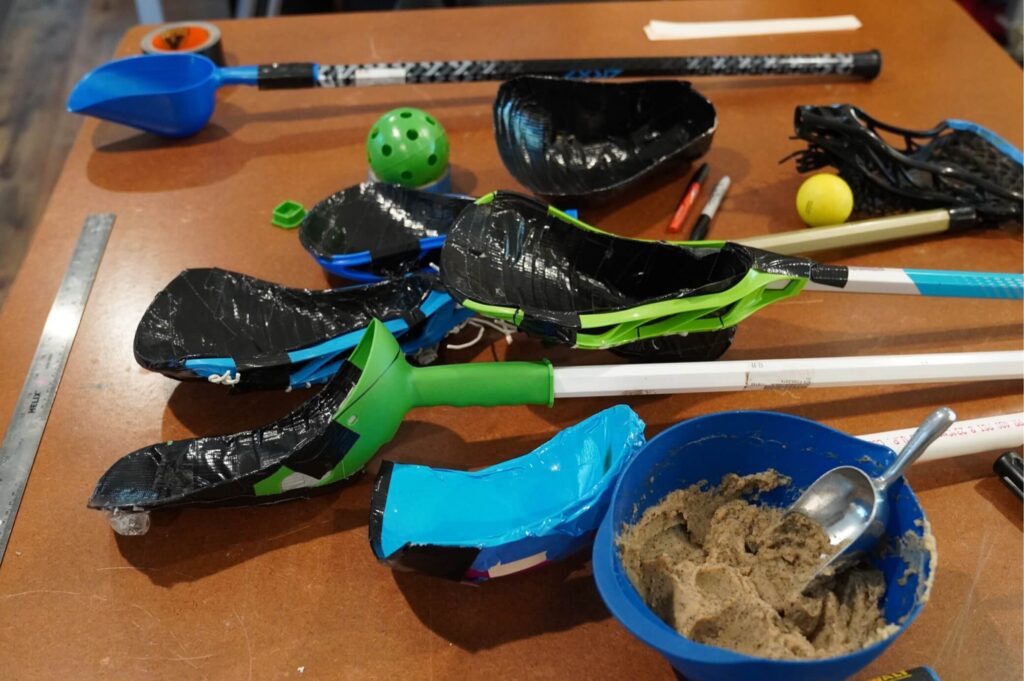
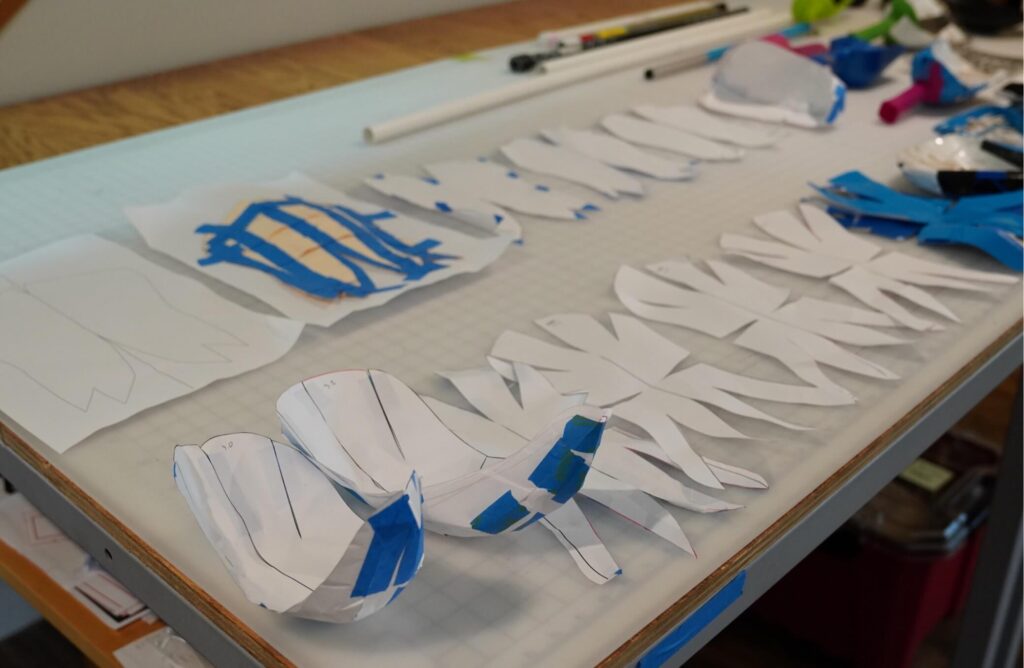
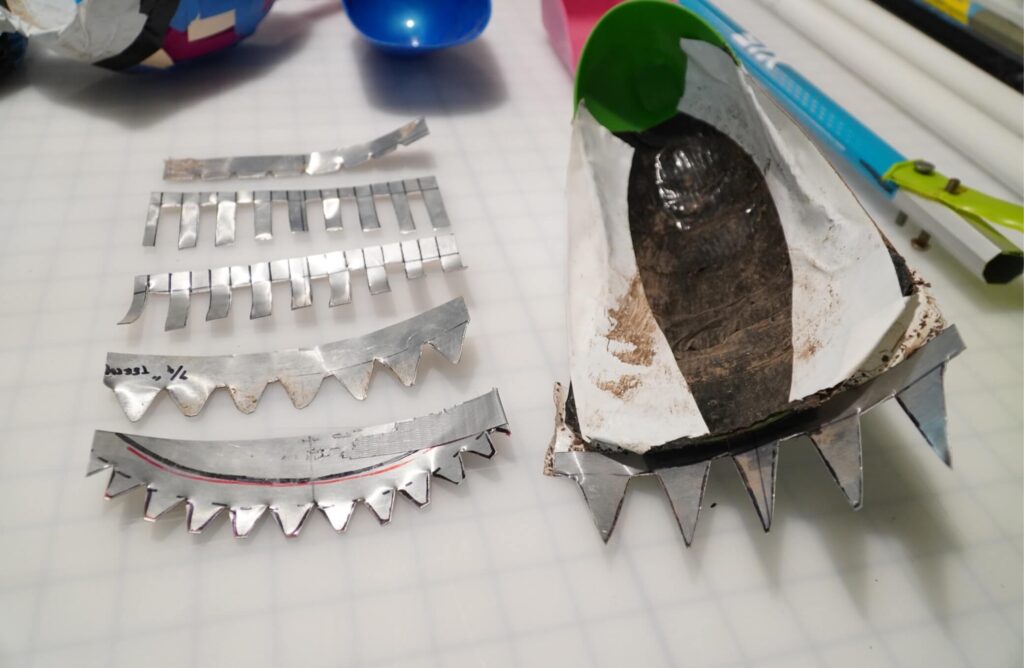
Ergonomics Testing
Products that interact with the body demand heavy prototyping and experimentation to get correct. A common saying in our studio is that “it’s easy to lie to yourself in a sketch”, so we like to move into physical 3D forms as early as possible. We often start with rough clay or sculpted foam models for validation of form and volume, then we move into 3D CAD when we’re ready to increase precision. Refining ergonomics as part of CAD development ensures that we can quickly adjust the models as user testing feedback comes in.
Testing and refining 3D CAD models throughout the development process allows the design team to know early on that the end user is going to have a positive experience with the product, driving positive responses and product reviews after launch.
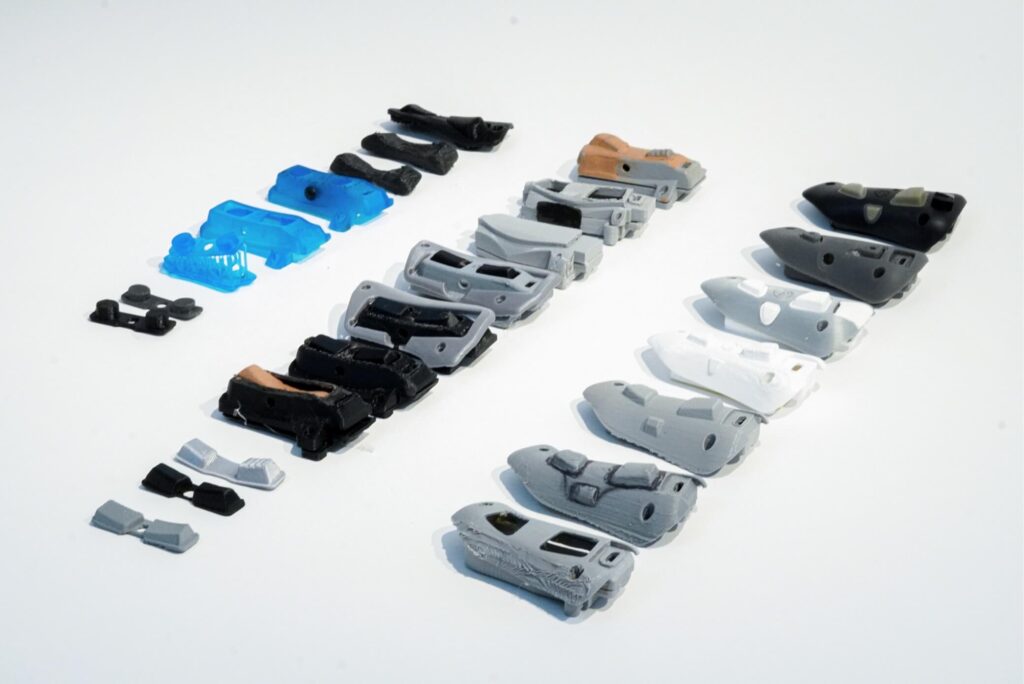
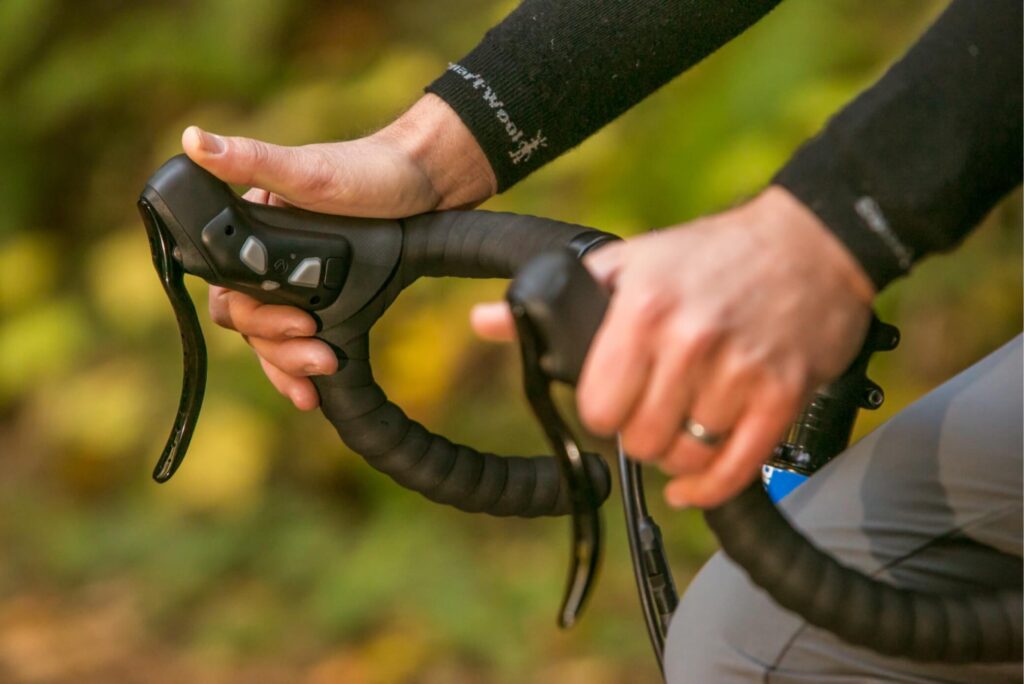